Die
A die is a metal perforated shape unit with holes, which is used to force raw material into pellets. In general, the holes and thickness of the die determine the final characters of pellets. Different size of the hole is provided, we have sizes from 2.5mm to 12mm for various kinds of raw material and pellets. The length of pellets is adjustable according to the commuter’s needs.Roller
Installed on bearings, roller is a cylindrical shaped equipment. The main purpose of the roller is to help raw materials get into die holes. Therefore, the shape and construction of the roller is designed for preventing slippage of raw materials and to give a rough surface for better traction. That is to say, the only driving force on the roller assembly is the friction from contact with a very thin mat of feed between the die and roll.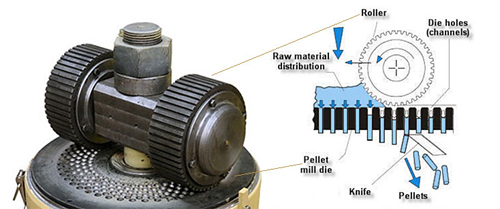
Bearings of Pellet Mills
Bearing are hidden in the mill where we can not see, so bearings do their work silently in tough environments. Nevertheless, bearings are crucial for the stable operation of machinery and ensure its top performance. The basic function of bearings is to reduce mechanical friction. Reducing friction means as follows. First, makes the mill runs more efficiently and smoothly. Second, less friction wear, thus extending the operating life of the machinery. Last, prevent abrasion burn, avoiding mechanical breakdown. During the pelletizing process, bearings basically help the shaft to rotate easily. Also, bearings contribute to lowering energy consumption and allow efficient transmission of power.Problems and solutions
The first use of a brand new die, the distance between the roller and die is either too large or too small, serious wear and tear of the die and the roller, raw material moisture is too high or too low. Above problems will cause a series of malfunctions as follows:1. Significant reduction in production, probably without output.
2. Rough surfaces of pellets.
3. Formation of pellets is difficult.
4. The pellet mill makes abnormal sounds.
5.Suddenly stopped while it is working.
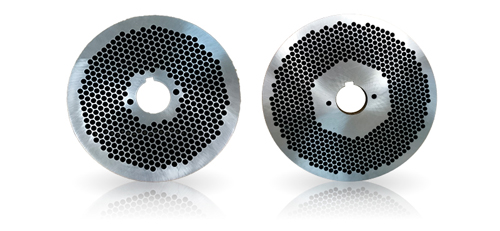
If you encounter above situations, first of all, shut down the machine and turn off the power. Make sure the die is not a new one, because these holes are not enough lubrication and it takes time to adjust.Ensure the proper moisture content of raw materials.Adjust the gap between the roller and the die. The gap generally should be between 0.05 mm and 0.3 mm.The roller or the die wears serious, replace a new one. Check other spares and make sure they can work well.Remove the foreign body to ensure material in and pellets out smoothly.
Daily maintenance
- Check the die and roller each time before using to ensure that there is no foreign body or breakage in the die or roller. The working life of the die under normal operating conditions is 300-500 hours, the die can be replaced after the abrasion of both sides.
- Keep the dies and rollers in a cool dry place. Any metallic parts has a strong tendency to rust if exposed to air and damp.The wood chips filled in the die holes absorb and maintain moisture, which will accelerate the corrosion process and cause reduction of the service life, resulting in low production efficiency.
- If you need to remove the die and roller in work of a pellet mill and then store them. Cleaning is necessary, clean up the residue like sawdust, wood chip. Extra pellets left in the die holes will speed up the corrosion.
- Fill in the holes with oil mixture(mixture of raw material and 10% wasted engine oil). This will ensure the not blocked and ready for the next running.